Overcoming Design And Manufacturing Constraints In Robotic Systems: Real-World Solutions
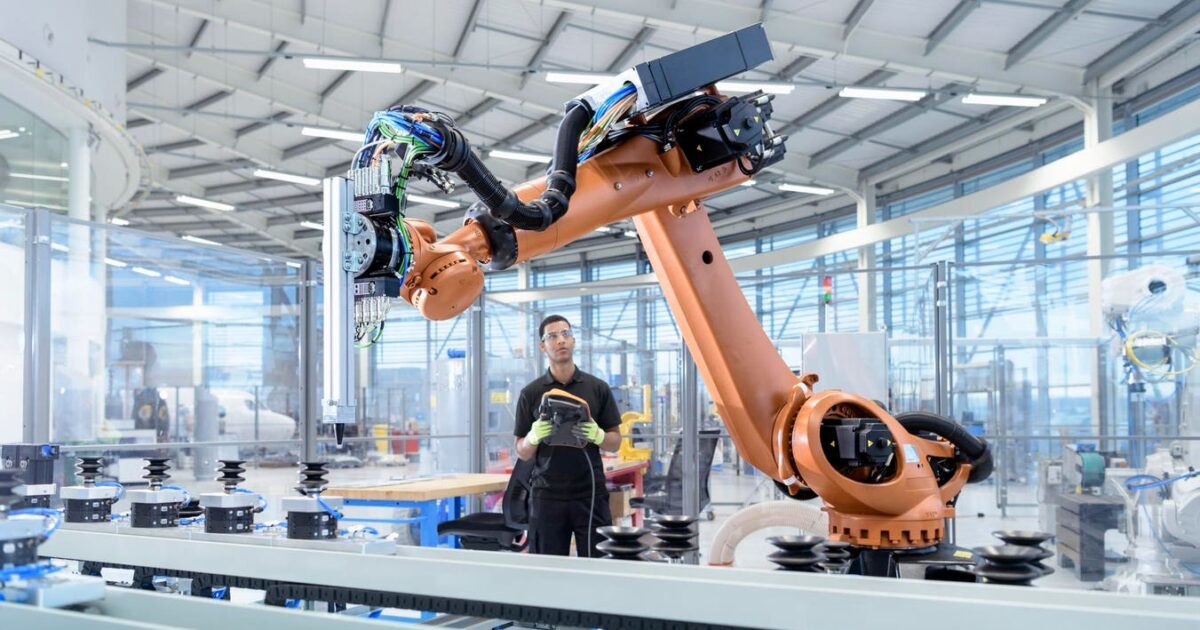
Jay Shah is a Lead Hardware Engineer at Caldo, specializing in robotics, automation, and sustainable food technology.
Robotic systems are transforming industries worldwide, from manufacturing plants to healthcare facilities. However, the journey from concept to deployment is often fraught with design and manufacturing constraints. These challenges can delay progress, increase costs and limit robotics’ full potential.
In this article, we’ll explore the key constraints robotic system developers face and how these can be overcome, supported by real-life examples.
Design Constraints in Robotic Systems
One of the primary challenges in designing robotic systems is ensuring they can perform tasks with high precision, flexibility and reliability. Robotic systems need to integrate complex technologies like sensors, actuators and controllers while also operating within the physical limitations of their environment.
Space Constraints: Many industries demand compact robotic systems that fit into small spaces without compromising functionality. For example, in healthcare, surgical robots must operate in the constrained environment of an operating room while maintaining extreme precision and reliability.
Complex Interactions: Robotics systems often need to interact with humans or other machines. Achieving safe, effective interaction in dynamic, unpredictable environments remains a significant design challenge. These systems must be able to make real-time decisions based on varying input, which requires sophisticated algorithms and sensor technologies.
Manufacturing Constraints
Manufacturing robotic systems introduces its own set of constraints, primarily focused on material selection, production scale and quality assurance.
Material Limitations: Robotic systems must be durable enough to withstand the stresses of daily use while being lightweight for mobility and energy efficiency. Choosing the right materials is key, and the wrong choice can lead to failures in performance or longevity.
Production Scalability: Robotics systems, especially those used in high-volume industries, need to be manufactured at scale. This presents constraints in terms of consistency, speed and cost-effectiveness. For example, creating complex robotic systems with highly intricate parts can make mass production difficult without sacrificing quality.
Quality Assurance and Testing: Ensuring that a robotic system meets safety standards and works reliably in real-world environments requires rigorous testing. Robotic systems often go through multiple prototypes and iterations before the final product is ready, leading to longer lead times and higher costs.
Overcoming The Constraints
While these constraints can be daunting, numerous strategies can help overcome them, leading to better-performing robotic systems at scale. These strategies typically involve advanced technologies, innovative design methodologies and a focus on continuous testing.
Design Flexibility And Modularity
One approach to overcoming design constraints is modularity. By designing robotic systems as modular units, manufacturers can create customizable robots that can easily adapt to different tasks or environments. This flexibility not only reduces the cost of redesigning systems but also allows for faster deployment.
Example: ABB’s robotic arms used in manufacturing are designed to be highly modular, allowing users to swap out components based on the specific requirements of the task at hand. This design flexibility reduces costs and allows for rapid reconfiguration in various manufacturing environments.
Advanced Materials And Manufacturing Techniques
To overcome material limitations, companies are turning to advanced materials such as carbon fiber composites and titanium alloys. These materials provide a combination of lightweight properties and extreme durability, allowing robots to perform in demanding environments.
Example: Boston Dynamics’ Spot robot, a four-legged robot used for various applications such as industrial inspections, uses a lightweight aluminum frame combined with advanced composites to ensure durability without sacrificing mobility. The use of advanced materials enables Spot to carry heavy loads, navigate rough terrain and operate for extended periods.
Leveraging Automation and AI
Manufacturers can also overcome scalability constraints by implementing automation and AI. These technologies not only streamline production but also enable real-time monitoring of robotic systems, ensuring that quality standards are met and potential issues are identified before they become problems.
Robotic systems that incorporate machine learning and artificial intelligence are capable of improving their performance over time. This adaptability allows them to optimize their functions based on the feedback they receive from their environment, overcoming previous limitations.
Real-World Solutions: Overcoming Manufacturing Constraints
One of the most significant examples of overcoming manufacturing constraints comes from Tesla’s Gigafactory. Tesla utilizes highly automated production lines to manufacture robots and other systems at scale, using AI-driven processes to ensure consistency and minimize errors. By relying on automation, Tesla has reduced production time and improved efficiency, even for highly complex robotic systems.
Similarly, KUKA, a German manufacturer of industrial robots, has implemented 3D printing technologies to create complex parts for robots. 3D printing allows them to bypass some of the traditional manufacturing constraints of using molds and mass-production techniques. This approach reduces costs and lead times while increasing design flexibility.
The Future Of Robotics: Overcoming Constraints Through Innovation
The future of robotics will likely see even more advanced materials, smarter AI algorithms and improved manufacturing techniques. As robotic systems become more intelligent, their design and manufacturing constraints will continue to evolve, offering new opportunities for overcoming traditional barriers.
To stay ahead in this rapidly developing field, companies will need to focus on creating adaptable, modular systems that are capable of interacting safely with humans and other machines. By continuing to innovate and pushing the boundaries of what’s possible with design and manufacturing techniques, the robotics industry can overcome the constraints that once seemed insurmountable.
Conclusion
The constraints around designing and manufacturing robotic systems present significant challenges, but through innovation and the application of new technologies, they can be overcome. By leveraging modular design, advanced materials, and AI-driven production processes, companies like ABB, Boston Dynamics, Tesla, and KUKA are leading the way in overcoming these barriers. As the industry continues to evolve, the future of robotics looks brighter than ever.
Forbes Technology Council is an invitation-only community for world-class CIOs, CTOs and technology executives. Do I qualify?