Anaergia Gas Powers The Toyota Trigen Plant.
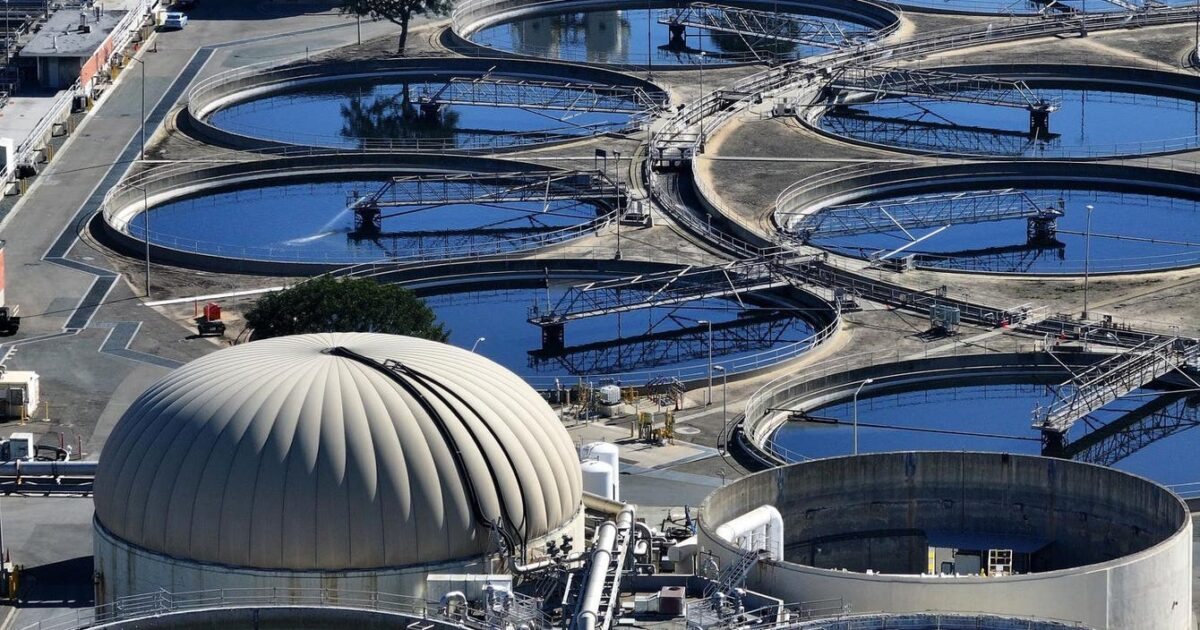
Anaergia anaerobic digester operations at the Victor Valley Water Reclamation Authority wastewater … More
What happens to all the food waste? Too often, it ends up in landfills—taking up valuable space and producing foul-smelling landfill gas rich in methane and carbon dioxide. Both are potent greenhouse gases that significantly contribute to climate change. In Los Angeles County alone, a staggering 11.1 million tons of organic waste are sent to landfills each year—and food waste makes up about 21%. But is there a better way? Anaergia just might have the answer–renewable natural gas (RNG). What is even better for this story, the Anaergia’s plant powers the Toyota Tri-gen Plant, which was introduced last year.
The Tri-gen facility was developed by Fuel Cell Energy (FCE) at Toyota’s Logistics Services terminal at the Port of Long Beach. This innovative plant produces electricity, hydrogen, and water using Anaergia’s RNG. At the heart of the facility is a 2.8 MW molten carbonate fuel cell, which internally process RNG into a blend of hydrogen, carbon dioxide, and steam. Approximately 70% of the hydrogen is used to generate 2.3 MW of net electricity, powering Toyota’s terminal operations. The remaining 30% is purified to yield up to 1,200 kg of fuel-grade hydrogen per day. From there, hydrogen flows to two adjacent refueling stations—one for hydrogen heavy-duty port trucks and the other for passenger vehicles like the Toyota Mirai. The byproduct water is used in the carwash before shipping to the dealerships.
Anaergia Inc. is a Canadian-based company in Burlington, Ontario, specializing in sustainable infrastructure by transforming organic waste into renewable energy. The company operates globally, delivering solutions across North America, Europe, and other regions. Anaergia’s technology portfolio includes advanced anaerobic digesters, biogas upgrading systems, and integrated waste management equipment. The company not only manufactures and installs this infrastructure but also provides full-service project financing, operations, and lifecycle support. Their projects enable municipalities and industries to comply with strict environmental regulations, like California’s SB 1383, while creating carbon-negative fuels.
In California, the Victorville Project, operated under Anaergia’s subsidiary SoCal Biomethane, is an award-winning, cutting-edge example of sustainable infrastructure retrofitting. It is located at the Victor Valley Water Reclamation Authority (VVWRA) wastewater treatment plant and supplies RNG to Fuel Cell Energy and Toyota Tri-Gen Plant.
Using Anaergia’s proprietary Omnivore™ digester technology and biogas upgrading systems, the Victor Valley facility co-digests sewage sludge and food waste—waste streams that would otherwise contribute significantly to methane GHG emissions. The plant converts 235,000 tons a year of waste and biosolids (140,000 gallons per day of wastewater biosolids and 20,000 gallons per day of external organic food waste) into 320,000 Mmbtu (94 GWh) of biomethane annually or 260 MWh daily.
“Anaergia is one of the world’s leading bioenergy developers, with more than a decade of experience converting organic waste and wastewater biogas into carbon negative power and fuels. Anaergia develops cutting edge projects that eliminate methane emissions from organic waste, which is the source of 87 percent of California’s methane emissions, and they are doing it successfully on four continents. Climate experts agree that methane reduction is the most urgent climate solution and Anaergia is making it happen.”— Julia Levin, Executive Director, Bioenergy Association of California.
Various waste and product technologies deployed by Anaergia.
Anaerobic digestion is a biological process that breaks down organic solids in the absence of oxygen, yielding biogas and a nutrient-rich digestate. At the core of Anaergia’s facilities is this process, enhanced by their proprietary Omnivore™ technology. Omnivore™ retrofits existing digesters to handle higher organic loading rates and co-digestion of multiple waste streams, making it a cost-effective upgrade for wastewater treatment plants. The digester tanks are designed to mimic the conditions of the human digestive system—warm, mixed, and anaerobic. Inside, microbial communities break down primary sludge (settled solids from sewage), secondary sludge (biomass from aerobic treatment), and high-energy food waste into biogas. This is particularly valuable in facilities like the one in Victorville, where both sewage sludge and food waste are processed together—an approach known as co-digestion. The facility is retrofitted to accept food waste trucked in from external sources—waste that would otherwise end up in landfills, which are the leading source of methane emissions in California. Food waste is highly energetic, as it hasn’t yet been metabolized, and represents a significant component by weight of landfill-bound material. Diverting this organic waste is critical to meeting methane reduction targets under state and international climate goals. To process the food waste, Anaergia employs proprietary equipment to remove residual contaminants, ensuring efficient and reliable digestion.
The next step is upgrading and conditioning of raw biogas—about 60% methane and 40% carbon dioxide— into RNG. The process begins with the removal of trace contaminants, including reduced sulfur compounds, volatile organic compounds, and moisture, using physical-chemical scrubbers and cooling, condensation systems. Once conditioned, the biogas undergoes a three-stage membrane separation process. This system takes advantage of the different diffusivities of CO₂ and methane, allowing for efficient recovery of methane at purity levels exceeding 99%. The final product is pipeline-grade RNG, indistinguishable from natural gas but with a negative carbon footprint. The gas is injected into the Southwest Gas utility pipeline. It is then used by FuelCell Energy as a feedstock for hydrogen and electricity production at the Port of Long Beach.
After the anaerobic digestion process, the remaining material—called digestate—is separated into solids and liquids. The organic solids, which were not converted to biogas, still contain valuable nutrients and are typically dried and repurposed as high-quality fertilizer. This sustainable reuse avoids landfill disposal and returns nutrients to agricultural use. At the Victorville facility, operational responsibilities are split: Anaergia handles the front-end systems, including feedstock intake and biogas processing, while the Victor Valley Water Reclamation Authority oversees digestate management, leveraging their longstanding wastewater operations. This collaboration ensures efficient resource use and regulatory compliance.
Anaergia contributes critical technologies and expertise to the success of its waste-to-energy projects. The company manufactures and implements key process components such as food waste cleaning systems that remove residual contamination, mixing equipment that improves digester efficiency, and membrane systems for biogas upgrading. Beyond equipment, Anaergia brings operational know-how that ensures the facilities run smoothly, safely, and at peak performance.