Construction Firms “Build With Intelligence Built-In”
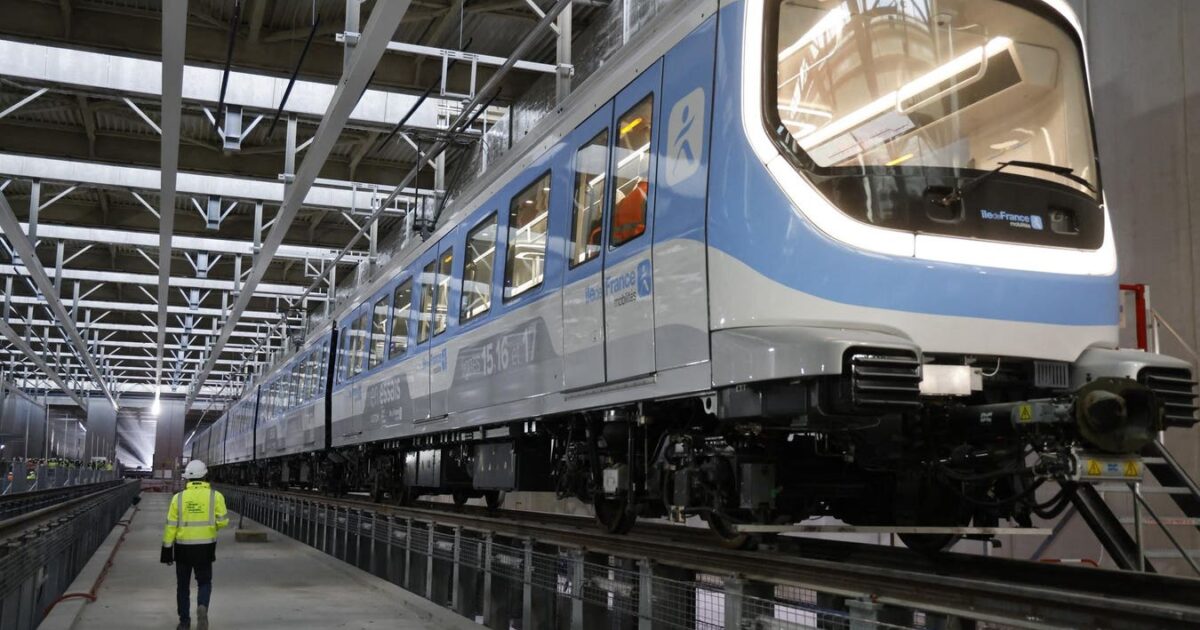
The first train of Line 15, part of the Grand Paris Express project, is pictured within its first … More
Construction megaprojects have a 91.5% failure rate—finishing late, over budget, or both. But a software breakthrough is changing this. It combines two existing technologies to create something new. Consider the $41 billion Grand Paris Express subway expansion.
One hundred feet below the streets of Paris, thousands of workers are building something massive. It will add four new lines to the city’s legendary Metro system. It’s 124 miles of new tunnels and 68 new stations. It’s Europe’s largest infrastructure project, the equivalent of adding the entirety of Washington, DC’s existing subway system.
The scale is staggering. In one recent week, 10,000 people were working. They had 50 miles of track and 25 stations under construction at the same time.
Projects this big usually fail. Less than 1% of big projects finish on time, on budget, and as planned.
But the Grand Paris Express project is different. They’re using a breakthrough that’s transforming how major construction and infrastructure get built.
The breakthrough combines two existing technologies. GIS (geographic information systems) maps the real world. BIM (building information modeling) shows construction details.
Separately, these tools are useful. Together, they’re revolutionary.
The fusion is not just a new tool, but a whole new way of designing and building things.
It creates something construction has never had: context and detail at the same time. Teams can see everything about where a project sits in the real world. They also see every detail about the project itself, down to individual wires and water connections.
For the Paris Metro, this means total visibility. Designers see every existing utility as they plan new rail lines. They know what cables can stay, what pipes must move. Construction teams can sequence work stages, plan material deliveries, and schedule the right workers.
The system also enhances “clash detection.” It spots where concrete pouring, electrical installation, and track construction will conflict with the built or natural world — or with each other. Then it suggests solutions before problems happen.
Everyone involved in the Grand Paris Express project sees the same information. Interior designers, city officials, lighting installers, problem-solving engineers, and community members all work from identical data.
Why Construction and Infrastructure Need This
By many measures, the construction industry is in crisis.
Rework alone—correcting things that have simply been done wrong—accounts for 12% of the cost of projects, on average.
A root cause? Communication and collaboration. Design changes get misunderstood. Field problems don’t get explained clearly to the office. Architects, engineers, and construction managers work in silos.
It’s frustrating to manage projects that get tangled in design disputes and construction delays. It’s frustrating to be the people trying to get those projects built on the ground. And it is doubly or triply frustrating to be the client: the person, or company, or city waiting for the tunnel to be finished or the office building to be ready, with the bill growing as unmet deadlines pass.
The combined GIS + BIM system helps tackle this. It creates “data continuity”—everyone using the same information about every element. It builds a digital bridge between field and office, between builders and designers and their clients. It speeds decisions while also giving everyone more confidence in those decisions. It’s designed to let architecture, engineering, and construction (AEC) firms fulfill their promises.
Thomas Lesage, digital transformation officer for the French firm, Egis, managing the construction of the Grand Paris Express, calls using the system “a pleasure.”
Building with Intelligence
Other projects see similar results. Peru used it to rebuild flood damage across an area four times the size of New York City. Until the convergence of GIS and BIM, no software system could handle the data and users for such a dispersed effort, with so many contractors and so many stakeholders across such a wide geography. Engineer David Castillo called the system built using GIS + BIM the project’s “greatest achievement.”
It’s the flexibility and adaptability that makes unifying GIS and BIM so valuable. It shows the reality, the plan, and it can model the future—or several different possible futures, depending on everything from climate to funding.
San Francisco International Airport used it to rebuild Terminal 1 during the pandemic. They don’t call it a “digital twin”—they call it a “dynamic twin” because it adapts in real time.
This transformation in construction matters all the more because construction has a massive impact on the world. Buildings create 42% of global carbon emissions. Globally, we’re constructing the equivalent of the building space in New York City every month—and will continue to do so for 40 years.
A dozen New York Cities of new construction a year.
We can’t afford the current 91.5% failure rate. Every delayed project wastes resources. Every cost overrun cuts profits. Every mistake creates more emissions.
The world needs smart construction. Projects that work the first time. That take into consideration the place they’re being built. That meet both economic and environmental needs. Buildings designed for both today and 40 years from now.
The GIS + BIM fusion doesn’t just make better projects. It makes better processes and better places. It helps people work together faster and more naturally.
The technology combines trusted tools companies already use.
Early adopters say it transforms company culture, not just project outcomes.
As one AEC management veteran said: “We are nullifying the frustration.”
For an industry swimming in frustration, that’s revolutionary.
Learn more about how the AEC industry is leading the way forward to solve today’s biggest infrastructure challenges using GIS technology.